News
Media and articles of interest
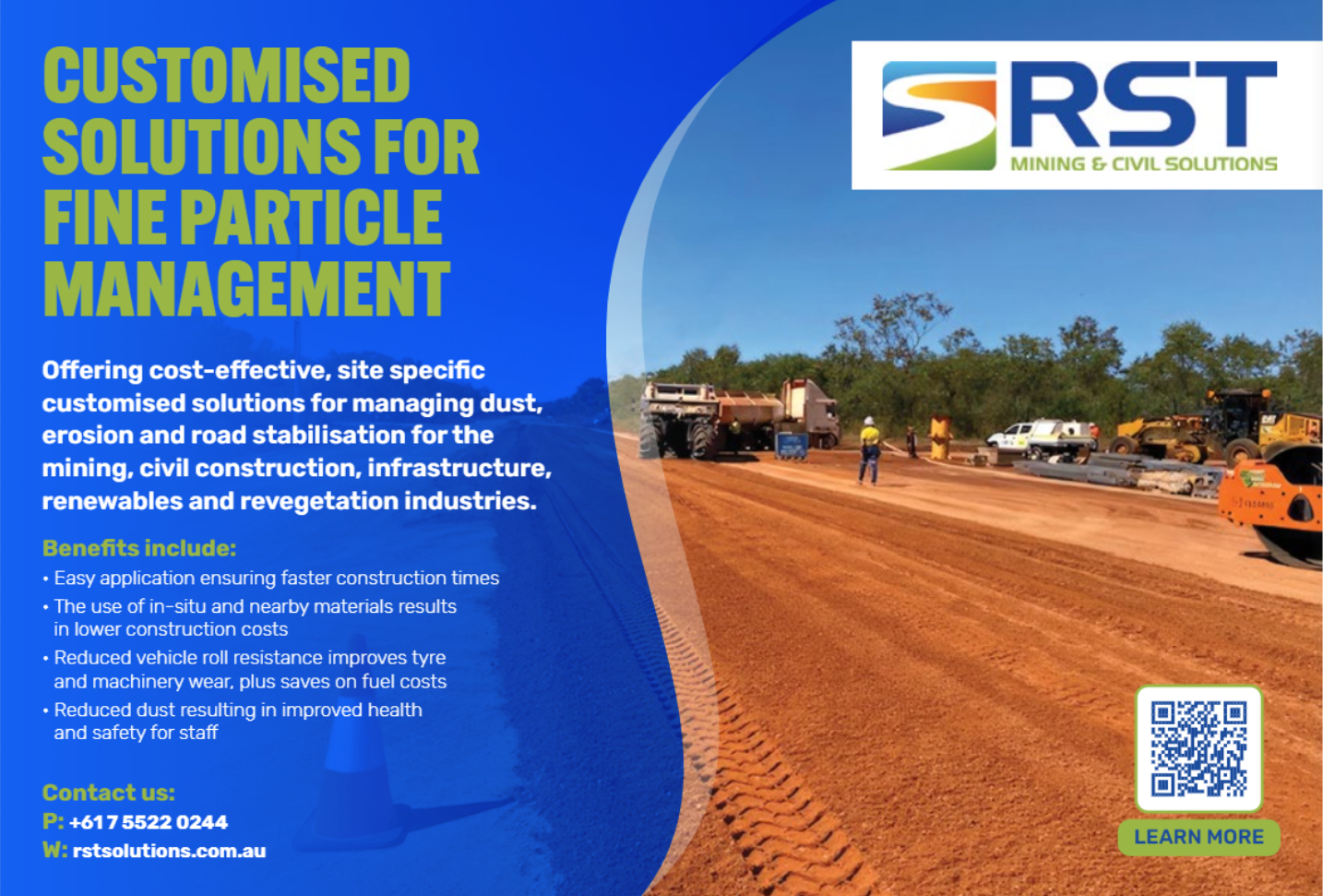
RST MINING & CIVIL SOLUTIONS PROVIDING ADVANCED SERVICES TO THUNDERBIRD MINERAL SANDS MINE
Advanced road stabilising technologies developed by Reynolds Soil Technologies (RST Solutions) were used at Thunderbird Mineral Sands mine to assist in constructing 34km of high
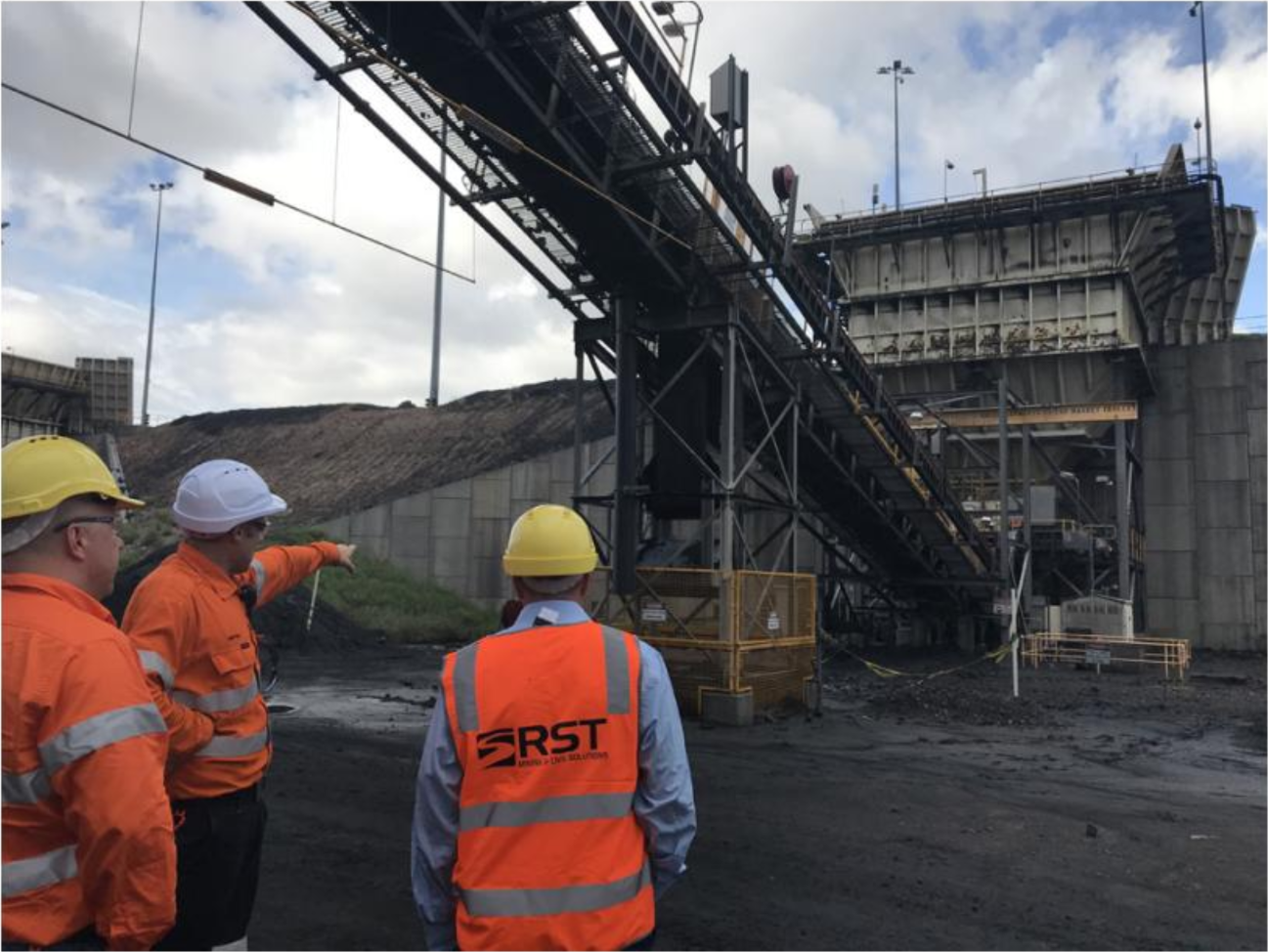
THE DEM Sweet Spot
Lee Gailer, RST Solutions, Australia, outlines how to achieve ideal moisture levels for controlling dust while using less water to preserve product quality. Increased focus
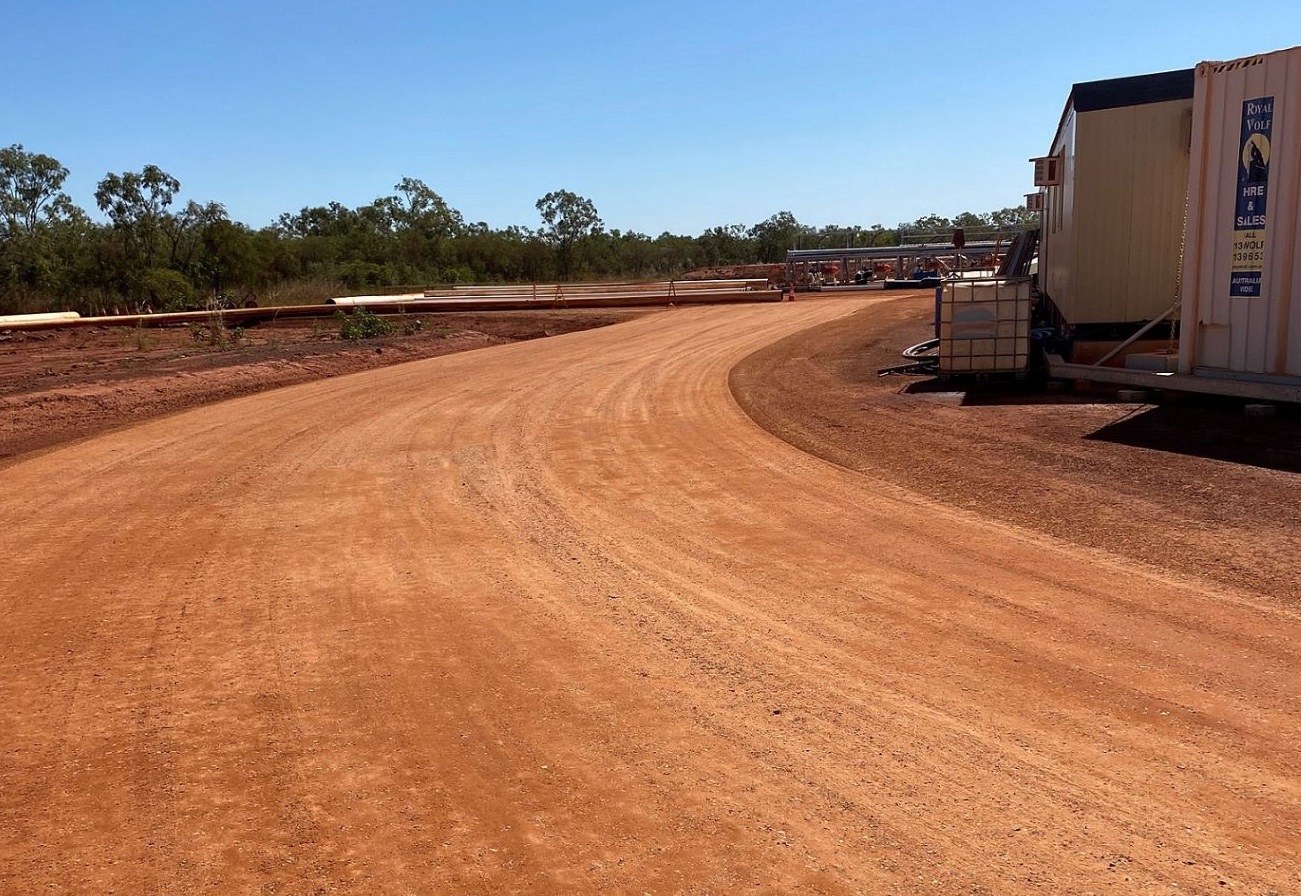
RST solves road construction project issue for Australian mine
A challenging road construction project for a new Australian mine has achieved success using advanced road stabilising technologies from Reynolds Soil Technologies (RST Solutions) to
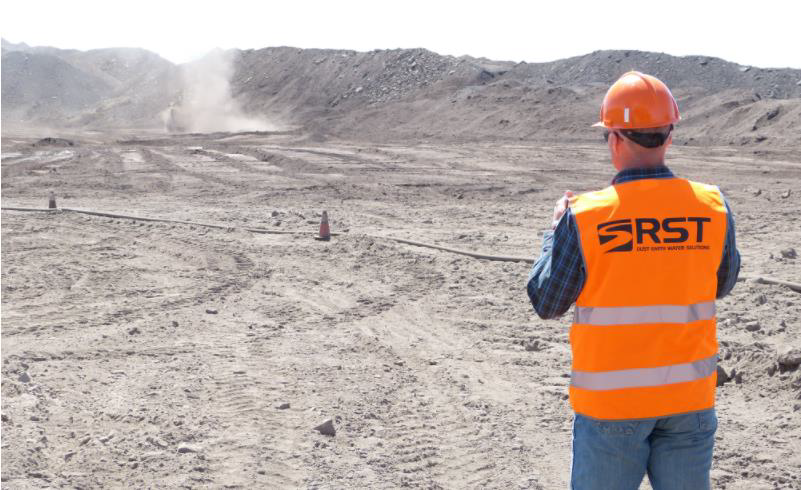
Lead Fine Particle Specialist RST Aims for maximum Dust Suppression with a Holistic Approach
The ability for a company to aum for maximum dust suppression relies on a holistic approach to the supply of solutions, combining different methods